Lean zur Gewohnheit machen
Warum Start-ups in die Lean-Falle tappen
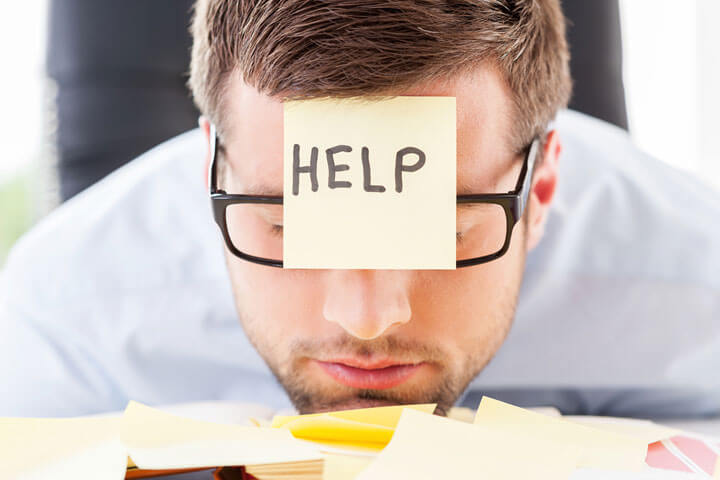
Lean ist das Erfolgsgeheimnis für Unternehmen. Toyota hat es vorgemacht. Und so hat sich in den Köpfen eingebrannt: „Wir (über)nehmen die Methoden von Toyota – und schon stellt sich der Erfolg in der Produktion ein!“ Gegen den Erfolg gibt es schließlich keine Argumente, der Erfolg gibt Recht. So einfach ist es natürlich nicht. Viele Unternehmen beginnen, sich mit Lean zu beschäftigen – und sind nicht erfolgreich. Woran liegt das?
Die meisten Unternehmen beginnen damit, die sogenannten Lean-Methoden einzuführen. Besonders beliebt ist die Methode 5?S, eine Methode zur besseren Arbeitsplatzgestaltung. Hierbei werden die Arbeitsplätze aufgeräumt und neue Standards für Ordnung und Sauberkeit geschaffen. Gleich danach führt das Unternehmen das Kanban-Prinzip ein – die Führungskräfte und Mitarbeiter sind nun fleißig damit beschäftigt, Prozesse zu analysieren und zu optimieren.
Schließlich wird das Rüsten – gemeint ist die Zeit für Einstellungen und Vorbereitungen einer Maschine, damit sie dann einen bestimmten Werkstoff produzieren oder bearbeiten kann – optimiert und mit den Lean-Werkzeugen ›Total Productive Maintenance‹ oder ›Total Productive Management‹ daran gearbeitet, die Maschinenverfügbarkeit zu verbessern. Die kontinuierliche Verbesserung ist ein Ansatz, der besonders viele Anhänger findet.
So weit, so gut. Fast immer haben diese Methoden zu Beginn Erfolg. Das Unternehmen freut sich über messbare Verbesserungen – und so wähnt sich die Unternehmensführung auf einem guten Weg zum leanen oder schlanken Unternehmen. Aber die Freude währt in der Regel nicht lange. Oft wird es schon bald mühsam, Lean stagniert und es geht nicht mehr voran. Das Engagement der Mitarbeiter lässt nach und die Ergebnisse bleiben aus. Das Unternehmen ist in die Lean-Falle getappt.
Gründe für das Scheitern – und wie Sie es vermeiden
Lean-Falle bedeutet, dass es trotz aller guten Absichten nicht gelungen ist, die Ziele zu erreichen, die sich das Unternehmen bei der Einführung von Lean gesetzt hat. Das kann ganz unterschiedliche Ursachen haben.
Lean-Falle 1: Lean geht nicht nebenher
Wer sich lediglich einige Aspekte aus dem Gesamtkonzept heraussucht und umzusetzen versucht, wird scheitern. Lean geht nur ganz oder gar nicht. Die Konsequenz ist, dass sich die Unternehmensleitung sehr genau überlegen muss, was sie mit Lean erreichen will und wie es gelingen kann, im Laufe der Zeit alle Mitarbeiter im Unternehmen in die Arbeit an der Verschwendungsbeseitigung zu integrieren. Der Methodeneinsatz allein genügt nicht und wer mit dem Methodeneinsatz beginnt, zäumt das Pferd von hinten auf.
Die Folge: Es geht nach der Einführungsphase nicht mehr weiter voran mit Lean, die Dynamik geht verloren, der versuchte Wandel zum Lean schläft allmählich ein.
Merke: Lean ist eine Philosophie, die als Ganzes umgesetzt werden muss.
Lean-Falle 2: Übermäßige Ausweitung der Führungsspannen und ausgedünnte Hierarchien
Als Lean in den 1990er-Jahren in Deutschland bekannt wurde, verstanden die Unternehmensführungen vor allem, dass ›schlanke Führung‹ umgesetzt sein müsste, um lean zu sein. In der Folge dünnten viele ihre Hierarchien aus. In der Produktion verschwand entweder die Vorarbeiterebene oder es wurden die Meister abgeschafft.
Die fatale Folge war, dass die Führungsspanne der verbleibenden Führungskräfte drastisch stieg und kaum noch Zeit für die Betreuung der Mitarbeiter blieb. Die Führungskräfte hatten also immer weniger Zeit für ihre eigentliche Aufgabe: das Führen von Menschen.
Heute versteht man Lean auch in Deutschland besser:
Es zeigt sich, dass eine wirkungsvolle Beseitigung von Verschwendung im Unternehmen nur möglich ist, wenn es Führungskräfte gibt, die sich um die Mitarbeiter kümmern und vor Ort mit ihren Mitarbeitern gemeinsam die Prozesse verbessern.
Auf der Ebene der Teamleiter wird die Führungsspanne in vielen Unternehmen deutlich reduziert, damit wirkungsvolle Mitarbeiterführung wieder möglich wird.
Lean-Falle 3: Lean als Insellösung der Produktion
Wenn Lean lediglich in der Produktion realisiert wird, bleibt es eine Insel im Unternehmen. Die administrativen Bereiche bleiben außen vor und damit können die Prinzipien von Lean nicht im Unternehmen insgesamt greifen.
›Ganz oder gar nicht‹ – dieses Motto gilt auch für die Reichweite von Lean. Selbst wenn das Unternehmen versucht, das Lean-Konzept in der Fertigung nahezu vollständig zu verwirklichen, droht letzten Endes das Scheitern, wenn Lean nicht konsequent im gesamten Unternehmen verwirklicht wird.
Richtig ist zwar, dass es in den Angestelltenbereichen in der Regel sehr viel schwerer fällt, Lean einzuführen. Hier sind die Widerstände größer und die Veränderungen, die eingeführt werden müssen, oft gravierender. Dennoch sollte ein Unternehmen sein Lean-Vorhaben grundsätzlich überdenken, wenn es nicht den festen Willen hat, Lean im ganzen Unternehmen zu verankern. Das braucht viel Zeit, das kostet Geld. Aber wenn man nicht dazu bereit ist, beides zu investieren, werden sich keine Erfolge einstellen.
Lean-Falle 4: Lean wird halbherzig begonnen
Lean erfordert den ganzen Einsatz der Geschäftsführung und der Führungskräfte. Ohne deren Überzeugung wird es nicht gelingen, eine Lean-Kultur zu etablieren.
Merke: Es ist kein Zufall, dass Lean in den Unternehmen gelingt, in denen die Führungskräfte bereits die Erfahrung gemacht haben, dass Lean funktioniert und wie Lean funktioniert. Führungskräften, die diese Erfahrungen nicht gemacht haben, fällt es sehr schwer, zu verstehen, worauf es wirklich ankommt.
Das bedeutet natürlich nicht, dass ein Geschäftsführer, der Lean noch nicht kennt, von Anfang an chancenlos ist, wenn er Lean in seinem Unternehmen realisieren möchte. Es bedeutet aber, dass er sich sehr genau erkundigen muss, was Lean bedeutet und wie Lean funktioniert.
Dazu müssen Sie heutzutage nicht mehr nach Japan fliegen und Toyota besuchen. Viel mehr erfahren Sie, wenn Sie in hiesige Unternehmen fahren, die seit Jahren erfolgreich Lean praktizieren. Dort finden sich garantiert Überzeugungstäter, die auch Anfängern gerne mit Rat und Tat zur Seite stehen und dabei beraten, wie Lean als Gesamtkonzept passend gestaltet und eingeführt wird.
Es reicht auch nicht, (nur) Methodenexperten ins Haus zu holen, denn Lean ist eine Philosophie und kein Methodenwerkzeugkasten. Und darum benötigen Unternehmen auch Unterstützung dabei, die Lean-Kultur in Ihrem Unternehmen heimisch zu machen und die Strategie und den gesamten Zielprozess nach den Prinzipien von Lean zu gestalten.
Lean-Falle 5: Lean-Schmalspur-Führungskräfte statt echter und überzeugter Lean-Leader
Der Absturz in die Lean-Falle ist unvermeidlich, wenn die Führungskräfte Lean nicht vorleben. Lean umzusetzen setzt voraus, dass sich das gesamte Management begeistert mit Lean beschäftigt und die Lean-Kultur vorlebt. Dazu gehört auch, das coachende Führen von der Geschäftsführung bis zum Teamleiter zu etablieren und konsequent umzusetzen. Lean findet vor Ort statt, am Ort der Wertschöpfung. Zu Lean passen keine Führungskräfte, die den ganzen Tag in ihrem Büro sitzen und sich mit Zahlen beschäftigen. Zu Lean gehören zwingend Leader, die verstehen, was in den Prozessen passiert, die täglich mit ihren Mitarbeitern sprechen und verstehen, wo sich die Probleme verbergen. Und die sich persönlich davon überzeugen wollen, ob die getroffenen Maßnahmen wirklich greifen, und die ihre Mitarbeiter aktiv dabei unterstützen, Ideen zu finden und zu verwirklichen.
Zu Lean passen auch keine Führungskräfte, die unnahbar sind. Lean erfordert Leader, die klare Ziele haben und ihre Mitarbeiter für diese Ziele gewinnen. Lean braucht keine Führungskräfte, die nur nach Zahlen führen, sondern Leader, die sich im Gespräch mit ihren Mitarbeitern überzeugen, ob eine geplante Lösung wirklich funktioniert und die ihren Mitarbeitern ein deutliches Feedback geben, ob sie zufrieden sind oder nicht. Und die ihre Mitarbeiter ermutigen, weiter an den Problemthemen zu arbeiten und Hilfestellung dabei geben, eine gute Lösung, ja die beste Lösung zu finden und zu etablieren.
Merke
Lean verträgt keine Führungskräfte, die mit Vorliebe die Erfolge ihrer Mitarbeiter als ihre eigenen deklarieren. Lean braucht Leader, die ihre Mitarbeiter erfolgreich machen und sich darüber freuen, wenn diese Erfolg haben. Denn Erfolg motiviert und beflügelt die Mitarbeiter zu weiteren Leistungen, die Lean vorantreiben.
Lean-Falle 6: Die Motivation geht verloren
Häufig beobachten wir in unserer Beraterpraxis, dass Mitarbeiter nach anfänglicher Euphorie die Motivation verlieren, weil sie nicht erleben, dass die erarbeiteten Maßnahmen umgesetzt werden. Zu Beginn haben viele Mitarbeiter Berührungsängste: Lean ist anders, ganz anders. Lean bedeutet für viele Mitarbeiter eine massive Veränderung ihres Denkens und Handelns. Und viele Menschen mögen Veränderungen nicht so gerne. Das Gute an Lean ist allerdings, dass die meisten Lean-Methoden ziemlich einfach sind und gut funktionieren. Haben die Mitarbeiter möglichst am konkreten Thema gelernt, wie es funktioniert, dann wollen sie mehr davon. Sie erleben Erfolg, der sie motiviert. Umso heftiger fällt dann die negative Reaktion aus, wenn sie erleben müssen, dass ihre Lösungen nicht umgesetzt werden oder die Umsetzung elend lange dauert.
Merke: Lean verträgt keine langatmigen Prozeduren. Denn Langatmigkeit und Zähigkeit vernichten den Elan, der Lean nach vorne treibt. Wer Menschen dazu bringen möchte, sich auf Veränderungen einzulassen, braucht Schwung und Begeisterung – und erlebbare Umsetzungserfolge.
Das Gute an Lean ist, dass sich Erfolge oft relativ schnell einstellen, häufig in Pilotprojekten. Aber viele Unternehmen schaffen es nicht, diesen Schwung aufrechtzuerhalten. Es wird unterschätzt, wie viele Ressourcen erforderlich sind, um die Maßnahmen schnell umzusetzen. Und wenn die Erfolge ausbleiben oder sie sich erst nach längerer Zeit einstellen, kriechen die Mitarbeiter wieder in ihr Schneckenhäuschen zurück. Haben sie sich aber wieder zurückgezogen, fällt es doppelt schwer, sie wieder herauszulocken. Dann wird es sehr zäh, Lean umzusetzen und es erfordert sehr viel Energie seitens der Führungskräfte, den Prozess wieder neu anzustoßen und mit Elan zu versehen. Was übrig bleibt, ist eine traurige Lean-Ruine.
Lean-Falle 7: Übermaß an Troubleshooting
Viele Unternehmen schaffen es nicht, das tägliche Troubleshooting zu reduzieren und stattdessen die systematische Verbesserung von Produktionsprozessen voranzutreiben. Damit wird das Troubleshooting sogar zu einem der größten Lean-Killer. Der Übergang von einer Organisation, die ganz auf das kurzfristige Abstellen von Fehlern und Problemen konzentriert ist, zu einem Unternehmen, in dem Probleme systematisch analysiert und die Ursachen der Probleme nachhaltig abgestellt werden, ist sehr schwierig. Es ist wie ein Teufelskreis, aus dem die Mitarbeiter nur sehr schwer herauskommen, zumal sehr oft die langjährigen Mitarbeiter tief sitzende Automatismen im Umgang mit den Fehlern entwickelt haben und sich deshalb sehr schwer damit tun, Probleme gründlich zu analysieren und an die Wurzeln heranzugehen.
Das wiegt umso schwerer, wenn auch die Führungskräfte solche tief sitzenden Automatismen im Umgang mit Fehlern ausgebildet haben. Eine gut funktionierende Lean-Kultur braucht aber saubere Prozesse und Standards, die von allen Führungskräften und Mitarbeitern eingehalten werden.
Lean-Falle 8: Lean bleibt Stückwerk und Spielwiese von Lean-Coaches
Die Lean-Falle droht auch dann, wenn Lean nur ein Projekt bleibt und nicht zum durchgängigen Programm für das gesamte Unternehmen erhoben wird. Die meisten Unternehmen starten den Weg in Lean mit einem Projekt. Das ist zunächst einmal sinnvoll, weil im Projekt die vielfältigen Anforderungen der Einführung von Lean am ehesten zu bewältigen sind.
Aber das Unternehmen muss rechtzeitig dafür sorgen, dass der Übergang vom Projekt zum Programm gelingt. Lean muss zum Normalfall werden, zum gelebten Alltag für alle Mitarbeiter und Führungskräfte. Gelingt dies nicht, werden die Lean-Prinzipien nicht durchgängig gelebt. Der Kraftaufwand nimmt zu, ist zu hoch – Lean schläft irgendwann ein.
In vielen Unternehmen ist Lean das Aufgabenfeld von hauptamtlichen Lean-Coaches oder Lean-Experten. Sie kümmern sich darum, Verschwendungsbereiche zu erkennen und auszumerzen. Sie sind die Methodenexperten und unterstützen die Führungskräfte und Mitarbeiter dabei, die Prozesse zu optimieren. Diese Kollegen sind oft sehr engagierte Mitarbeiter und erwerben im Laufe der Zeit viel Erfahrung dabei, Verschwendung zu reduzieren – aber:
Merke: Auf Dauer lebt Lean nur, wenn die Führungskräfte die Verantwortung für die Optimierungsarbeit übernehmen und die Mitarbeiter mit der Zeit lernen, selbst die Methoden anzuwenden. Bleibt dies aus, fehlen der Antrieb von innen und die Verankerung von Lean im Verhalten aller Beteiligten.
Lean-Falle 9: Einzelkämpfertum statt Teamarbeit
Wenn Lean die Angelegenheit Einzelner bleibt, gelingt die Verankerung im Unternehmen nicht. Ohne Teamarbeit gibt es kein auf Dauer erfolgreiches Lean. Das beginnt bei den Führungskräften: Lean braucht Führungsteams, die gelernt haben, vertrauensvoll zusammenzuarbeiten, die ihre Konflikte austragen und zu gemeinsamen Lösungen kommen und gemeinsame Ziele erarbeiten, die das gesamte Unternehmen nach vorne bringen – und nicht nur ihren eigenen Verantwortungsbereich.
Lean braucht funktionierende Teamarbeit bei den Mitarbeitern. Der Einzelne kann sich noch so sehr bemühen, auf Dauer wird er mit seinen Bemühungen scheitern, Verschwendung zu reduzieren, wenn die anderen in seinem Umfeld nicht mitziehen. Lean braucht daher Mitarbeiter, die gemeinsam an ihren Zielen arbeiten sowie gemeinsam Standards entwickeln und einhalten wollen und können.
Merke: Kontinuierliche Verbesserung gelingt nur, wenn Teams nach dem Motto ›Stärken stärken – Schwächen schwächen‹ arbeiten und lernen, die jeweiligen Stärken des Einzelnen im Team zu nutzen und gemeinsam dafür Sorge tragen, dass die Schwäche des Einzelnen von anderen im Team aufgefangen wird.
Lean-Falle 10: Keine Automatismen und keine wirkliche Verinnerlichung des Lean-Gedankens
Ganz entscheidend für den Absturz in die Lean-Falle ist: Lean wird nicht zur Gewohnheit im Unternehmen, sondern bleibt ein Fremdkörper in einer Umgebung, in der die alten Gewohnheiten weiter bestehen. Die Folge ist, dass es nicht gelingt, die Lean-Prinzipien im Unternehmen und in den Köpfen der Menschen zu verwurzeln.
Lean zur Gewohnheit zu machen – das ist die wichtigste Aufgabe, wenn ein Unternehmen durch Lean auf Dauer Erfolg haben möchte.
Wir sind davon überzeugt, erst wenn Sie die Lean-Verhaltensweisen zu Automatismen weiterentwickelt haben, lebt Lean richtig und dauerhaft. Erst dann ist Lean Grundlage allen Denkens und Handelns im Unternehmen. Und erst dann stellt sich der Erfolg ein – und bleibt.
Raus aus der Lean-Falle
Mehr über die Lean-Falle im brandneuen Buch “Raus aus der Lean-Falle – Lean erfolgreich zur Gewohnheit machen”, dass von Albert Hurtz und Daniela Best verfasst wurde. In ihrem Buch zeigen, wie es gelingt, die Verhaltensweisen und Einstellungen von Führungskräften und Mitarbeitern zu verändern und Lean zu wahrem Leben zu erwecken. Unser Artikel “Warum Unternehmen in die Lean-Falle tappen – und wie sie ihr ausweichen” ist ein Auszug aus dem Buch. “Raus aus der Lean-Falle – Lean erfolgreich zur Gewohnheit machen” jetzt bei amazon.de bestellen.